Heat Treating Information
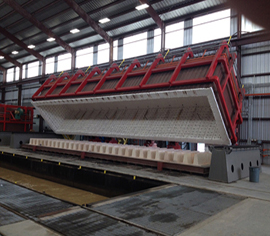
Batch Polymer & Water Quench Up To 58ft in Length.
We have the capacity to run batch heat treatment loads up to a maximum of 100,000 lbs - 58' in length with an overall load area of 96" wide and 48" in height at a maximum operating temperature of 1900 degree Fahrenheit.
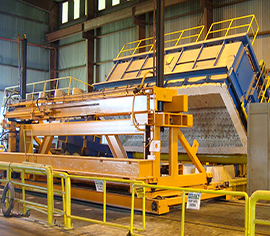
Batch Oil, Polymer & Water Quench 15ft & 25ft In Length
We have the capacity to run batch heat treatment loads up to a maximum of 30,000lbs - 25' in length with an overall load area of 72" wide and 42" in height at a maximum operating temperature of 2200 degree Fahrenheit.
Heat Treating Information
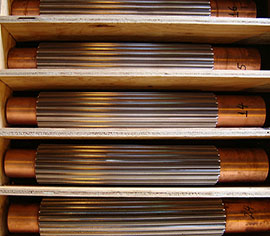
Atmosphere Capability
Horizontal atmospheric Carburizing, Carbonitriding, Solution Annealing, Aging, Normalizing, Hardening and Tempering, up to a Maximum of 30"High X 48" Wide X 84" in length with a 3,500lbs load capacity.
Oil or Water Quenching.
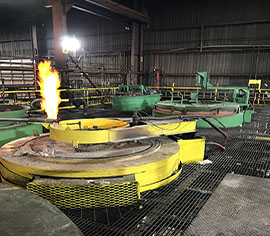
Vertical Capability
We have the capability to heat treat parts up to 41" diameter 120" long with a maximum weight of 4,000lbs per load.
Vertical atmospheric carburizing, solution annealing, aging, Normalizing Hardening and Tempering.
Polymer or Water Quench
Heat Treating Information
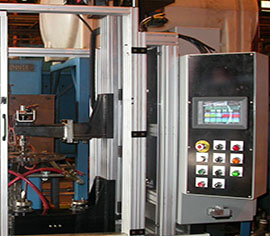
Induction Hardening
Lone Star has a fully equipped Induction Department. We have 4 state of the art N/C touch screen vertical scanners.
For deep case induction hardening we have a 125kw (10khz) power supply coupled with a vertical scanner capable of processing material up to 10 ft in length with 112" centers.
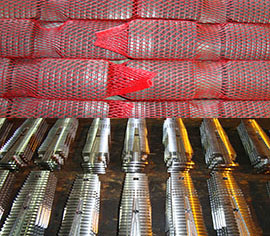
Benifits of Induction
The hardening process is used to produce a localized surface hardening of an area that needs wear-resistance, while retaining the toughness of the original structure as needed elsewhere. The depth of induction hardened patterns can be controlled through choice of induction-frequency, power-density and interaction time
Continuous Line Heat Treating
We installed our first continuous line in 1998 which proved to be a great addition to our facility. To increase capacity, a second continuous line was added in 2005.
Both lines are Bickley gas fired barrel type furnaces with high pressure water quenching and in line tempering, capable of running both bar and tube to high mechanical properties.
We have the capability of running Bar stock from 3" to 10" up to 42' long and Tube 3" to 11" up to 42' long.
Heat Treating in a continuous furnace gives you the added benefit of:
Stress Free Material.
Temperature Uniformity.
Control of Heating & Cooling Rates.
Repeatability of Process.
100% Inspection.
Metallurgical Quality.
After processing all material is tested in our Mechanical Testing Lab we are ISO/IEC 17025:2017 Accredited metallurgical lab for destructive & none destructive testing.
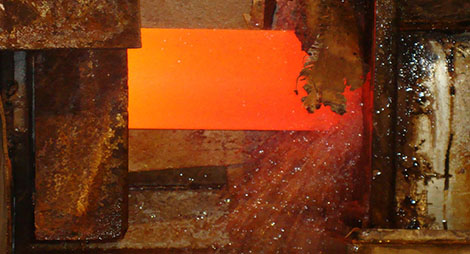
Heat Treating, U.T. Inspection, Lab Testing, Drilling, Delivery Service
Mechanical Testing Lab is ISO/IEC 17025:2017 Accredited.
Print Or View ISO/IEC 17025 Accredited Cert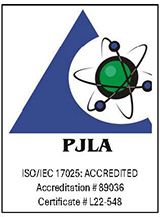
Our QMS is Certified to AS 9100
Print Or View AS 9100 Cert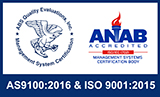